The product itself has to be innovative, and it has to do so within the existing category of consumers’ awareness.
Packaging is the icing on the cake for a good product, helping to take the brand and goods to the next level.
Product packaging design strategy
The product’s image and visual performance can attract consumers at first glance, leaving a good feeling and generating the desire to buy.
The brand invests limited budgets in the creativity of product packaging is the most economical and effective advertising method.
Because the packaging is the cultural carrier of the brand and is the best salesman of the product, a good packaging design can lead to the first purchase of consumers.
Thus the packaging strategy is to enhance the visual creativity of packaging design to promote sales.
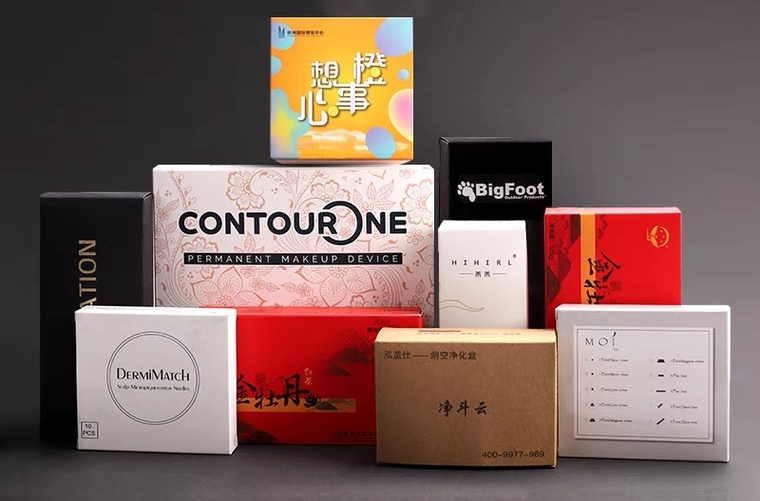
FMCG mainly depends on channels. And the brand only makes sense when it makes it more convenient for consumers to buy the goods.
A set of packaging designs with selling power can make the product sold efficiently. Most critically, it can directly make the consumer’s first purchase.
Strategies for creative product packaging design
The brand should determine the creative direction of packaging form and packaging design.
Firstly, the brand should conceptualize the eight contents: brand information, brand tone, sales channels, target consumer groups, product characteristics, product specifications and selling price, product market conditions, and product category life cycle.
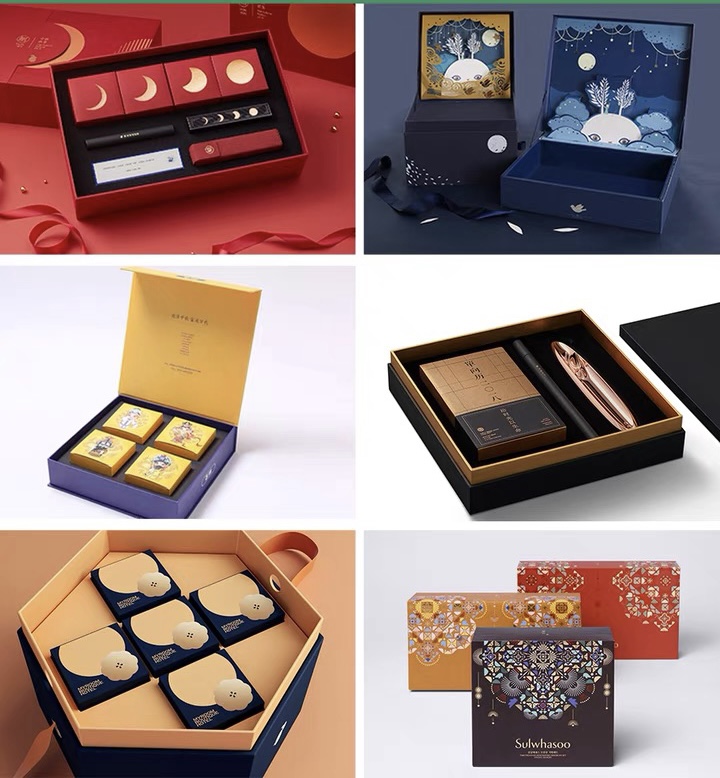
And then the brand should carry out the visual performance of the product packaging to make the packaging more innovative and attractive.
For multichannel products, online sales are a barometer of offline sales. Products with good offline sales will also have good online sales. Thus the e-commerce data are informative for the sales data of each brand’s product line in the offline channel.
How product packaging design influences your business
The first impression consumers have of a brand product is the visual elements of the packaging. Offline consumers understand the products through the introduction to the product’s outer packaging and on-site promoters.
Young and middle-aged people are the main force of online shopping and consumption. Online consumers are not only attracted by product packaging to the online store, but also by live promotional information, live video, and brand product details.
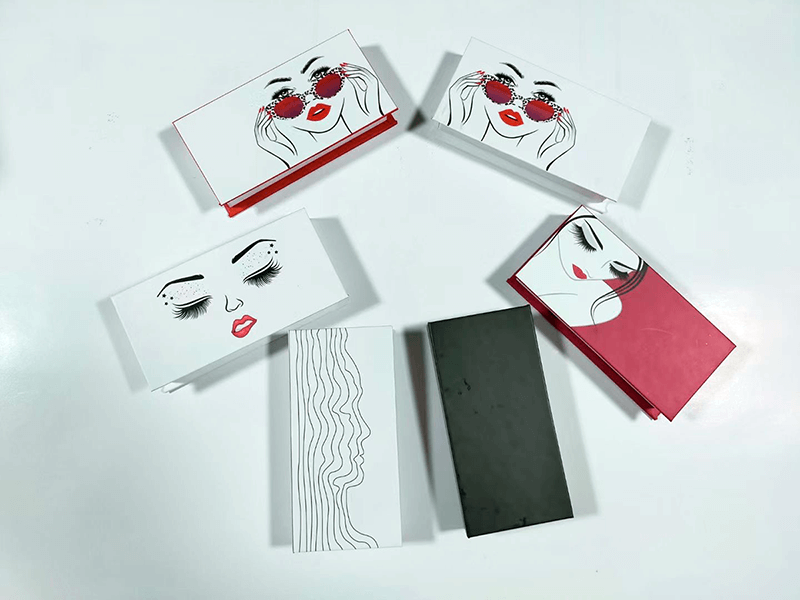
Among them, female consumers are the most willing to try the brand with a brand tone, with the pursuit of different styles, and focusing on the user’s sense of experience. The brand with an engaging story, beautiful and exciting outer packaging, and product’s practicality are the factors to impress female consumers to buy.
Common forms and materials of custom packaging design
FMCG products have their specifications for packaging, storage, load-bearing, and transportation.
There are already mature solutions that match the packaging ideas to make the packaging more marketable. The solutions include packaging functions, packaging planning, visual packaging design images, packaging materials, and box structures.
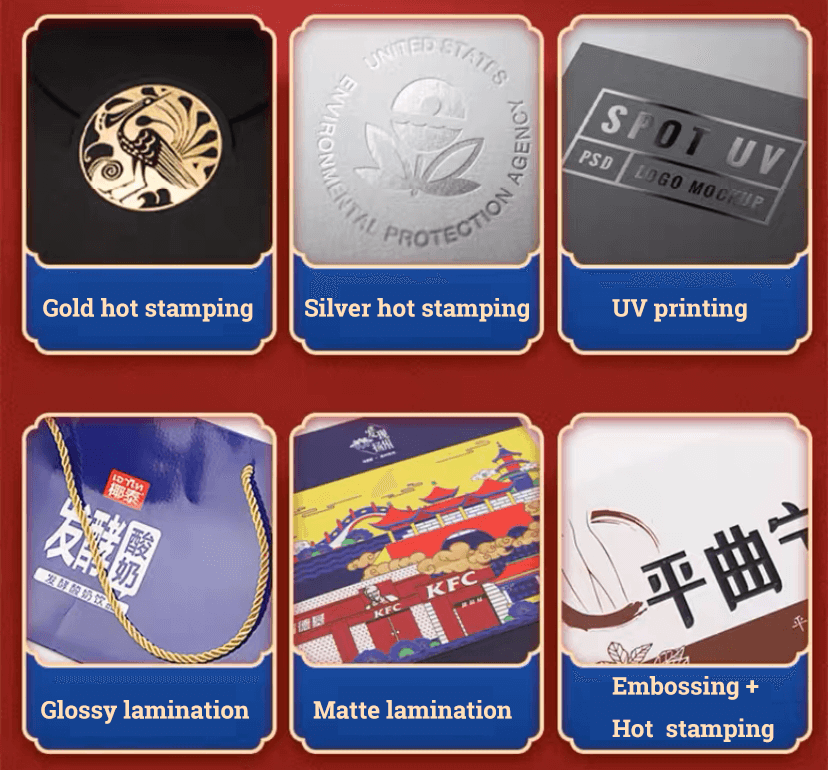
The selection of packaging materials should combine with the product’s characteristics, form, product grade and positioning of consumer groups, and other factors to select the appropriate packaging materials.
High-end products focus on the beauty and texture of the packaging materials, and common products focus on cost and practical. A variety of packaging forms makes products of greater diversity.
Types of product packaging by material
According to the packaging materials, the product packaging can be classified into two types: plastic flexible packaging and cardboard packaging.
Plastic flexible packaging
From the material, flexible plastic packaging has steamed bags, aluminum bags, vacuum bags, composite bags, etc.
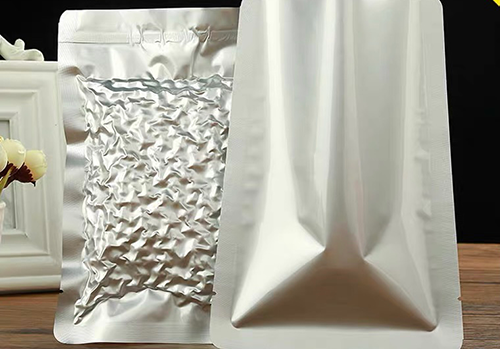
From the process, flexible plastic packaging has aluminum washing, striking gold, bright oil, matte oil, etc.
Cardboard packaging
According to the form of paper packaging, cardboard has two types: the paper roll and flat paper. Paper roll is for rotary printing; flat paper is usually cut into rectangular paper and used for most books, picture books, and posters.
Types of product packaging by application
According to the application, paper packaging can be classified into eight types as below.
Copperplate paper
Copperplate paper is a widely used printing paper because of its low price and good performance in color reproduction.
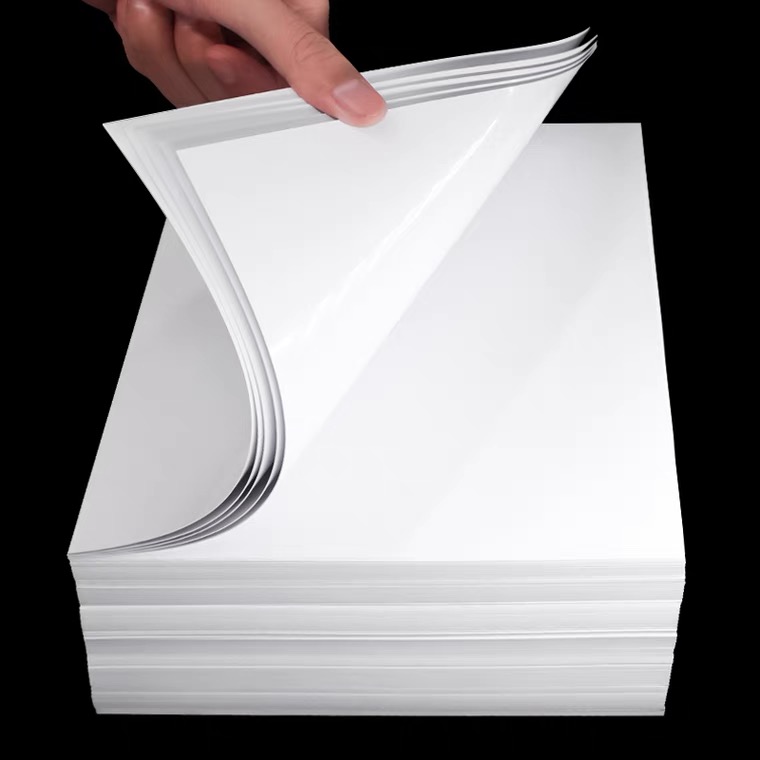
There are two types of copperplate paper, glossy and matte, with the weight of 128g, 157g, 200g, 250g, 300g, etc. It also can be classified into double-sided and single-sided coated paper.
Lightweight paper
Lightweight paper is a light offset paper, a more humane type of paper, with high quality and lightweight, low price, and environmental protection.
The original color can protect readers’ eyes, especially the elderly and children, to protect their eyesight from harm when reading.
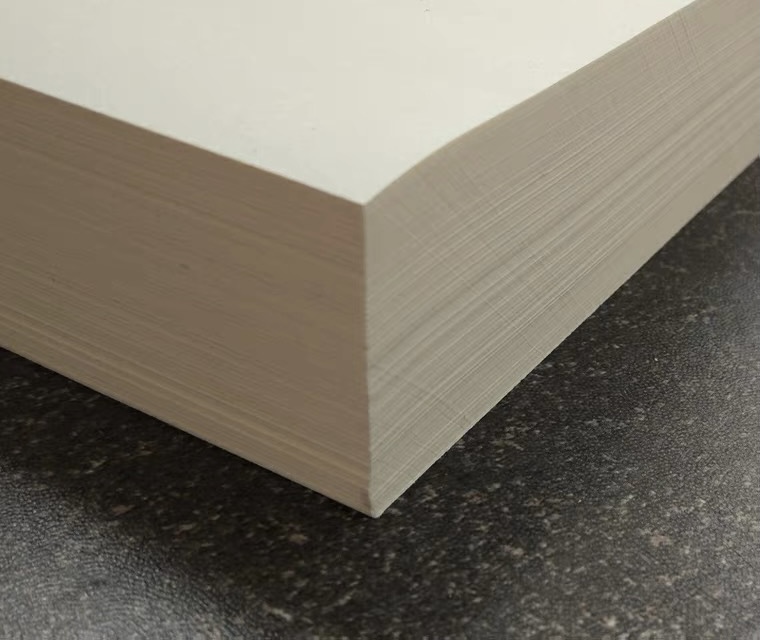
It is easy for readers to carry and read. The lightweight paper has a good texture and loose thickness, high opacity, good printing adaptability, and original reproduction after printing.
White cardboard
White cardboard is a thick paper with high weight and firmness and is often used in paper boxes.
White cardboard is high in whiteness and has high stiffness, breakage resistance, and smoothness, with a flat paper surface, no streaks or spots, and no warping or deformation.
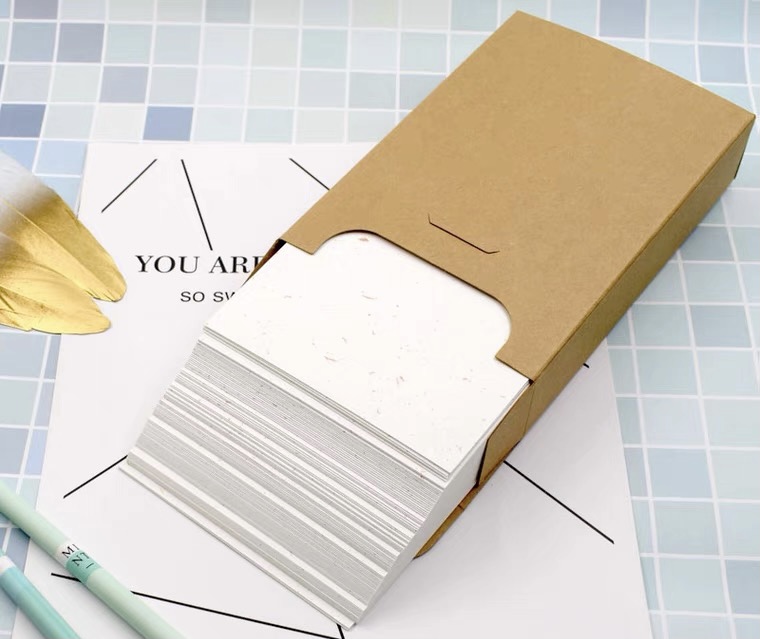
The weight of white cardboard is 200g, 220g, 250g, 270g, 300g, and 400g.
When making packaging, if you feel the gram weight is not thick enough, you can combine different weights of sheets. For example, you can laminate two sheets of white cardboard, such as laminating two sheets of 250-gram white cardboard into a 500-gram paper. It is usually used for large volume packaging.
Grey cardboard
Grey cardboard has a grey base color and a white-coated surface on the front side, and it is mainly used for packaging printing.
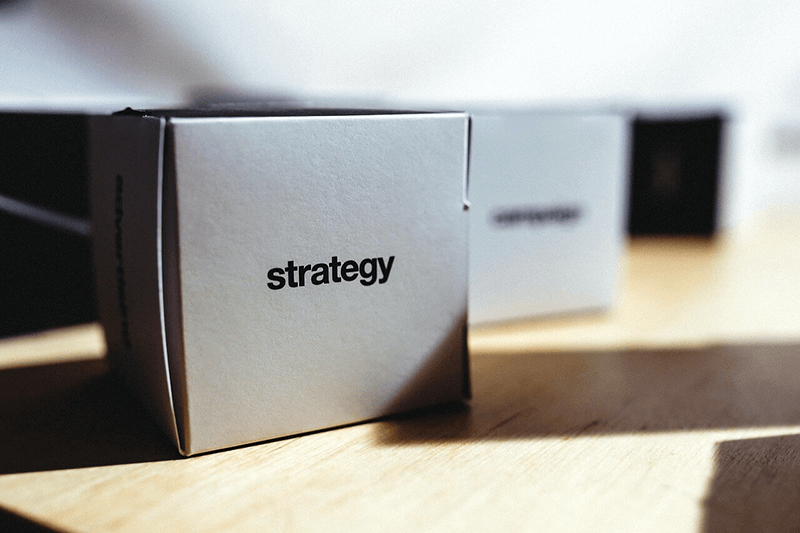
According to the material and the thickness of coated side, the grey cardboard paper has several types: A flute, B flute, C flute, E flute, and F flute.
Each flute is further divided into several grammages, which are divided into 200g, 230g, 250g, 270g, 300g, 350g, 400g, 450g, etc. Grey cardboard price is lower than the white card.
Sulfuric acid paper
Sulfuric acid paper is translucent, resistant to grease and water penetration, poor permeability, poor adsorption of ink, and color reproduction in the printing process.
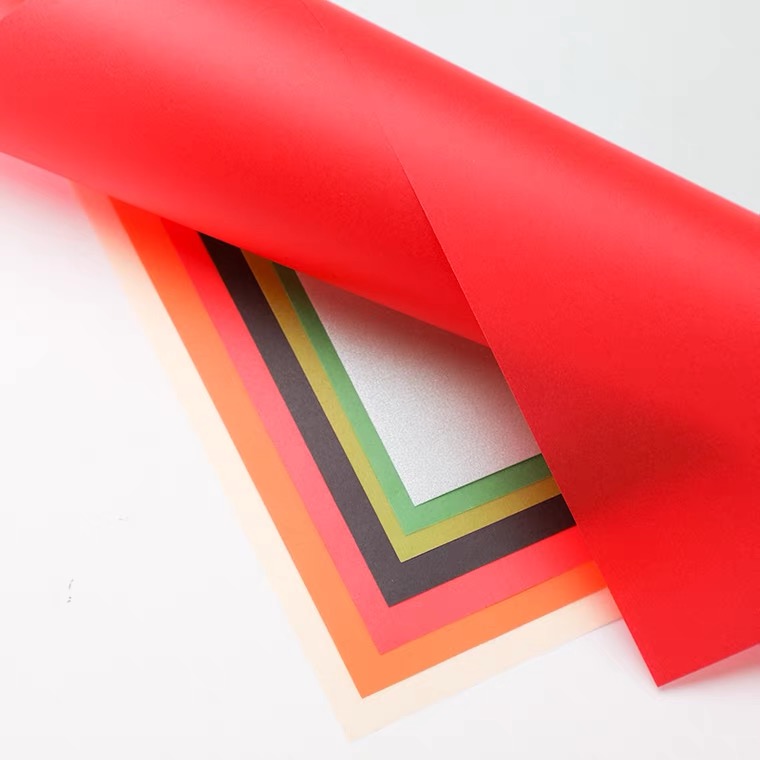
Sulfuric acid paper is a translucent medium specialized in engineering tracing and sun printing with an uncoated surface. It is sometimes used to bind books and as title pages for added effect.
In packaging, sulfuric acid paper is mainly used to cover products after opening the box, with a hazy aesthetic. Sulfuric acid paper is suitable for printing simple patterns in one color, not for printing complex patterns.
Kraft paper
Kraft paper itself has a certain toughness and strength and is often used as a packaging material. Its color is usually yellowish-brown. Semi-bleached or fully bleached Kraft pulp is light brown, cream, or white.
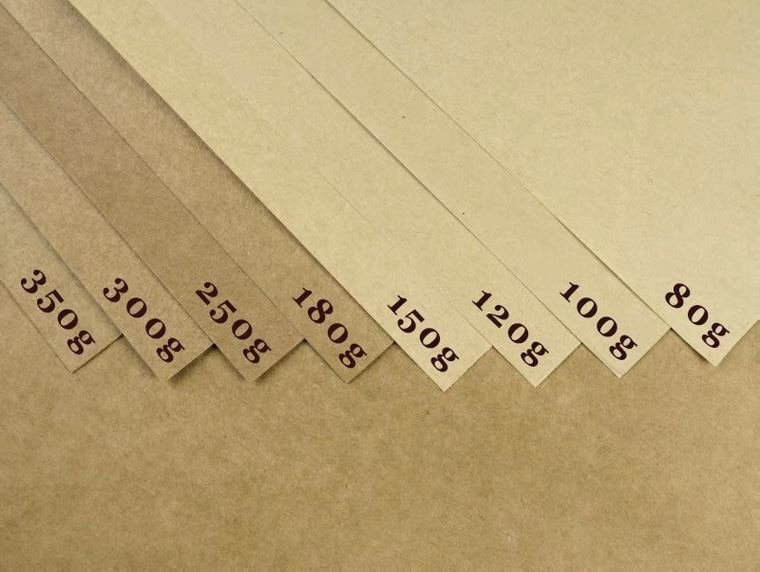
Kraft paper is mainly of rolls but is also available in flat sheets. It is made from sulfate coniferous wood pulp that is pulped and copied on a long-web paper machine.
Kraft paper can be printed directly. But it is not suitable for printing complex pictures due to the paper’s inherent dark color, high water absorption, and poor color reproduction.
If you want bright colors, you can print white first and then colorful patterns.
Corrugated cardboard
Corrugated cardboard is made of face paper, lining paper, core paper, and the corrugated paper that processed into waveform grooves.
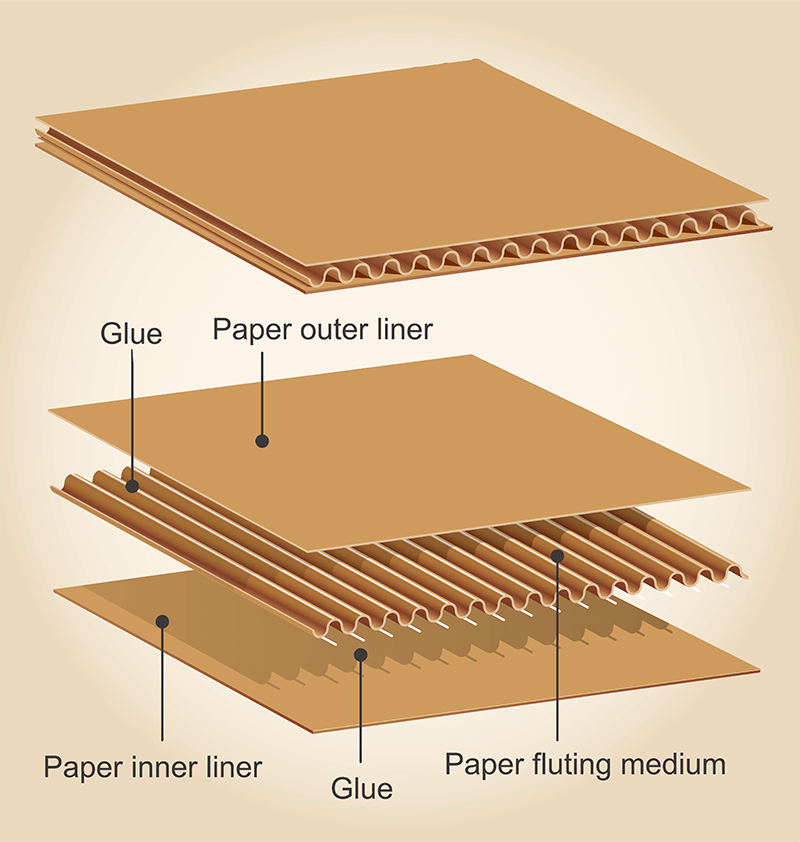
Specialty Paper
There are many varieties of specialty paper, and they are either textured or have a unique texture. Specialty paper is generally more expensive. Some specialty paper has very strong ink absorption, and week color reproduction.
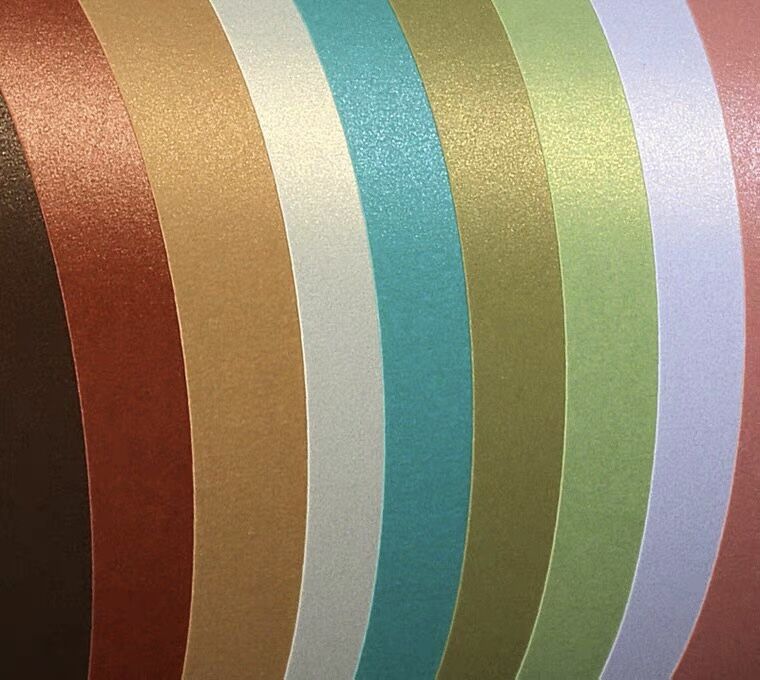
The large and thick texture specialty paper is simply not suitable or can not be printed.
Also note that do not print color patterns on dark specialty paper. At present, there are more and more types of paper, but the paper classification is not according to mandatory standards.
According to the application, the paper can be classified into cultural paper, packaging paper, household paper, industrial paper, military paper, and other specialty paper.
What types of corrugated cardboard are?
Corrugated cardboard has been invented and used for more than 100 years. Common corrugated cardboard is made of 3 layers, including one layer of fluting medium and two layers of flat liners.
Corrugated cardboard has the advantages of low cost, lightweight, easy processing, high strength, excellent print-ability, and easy storage and handling.
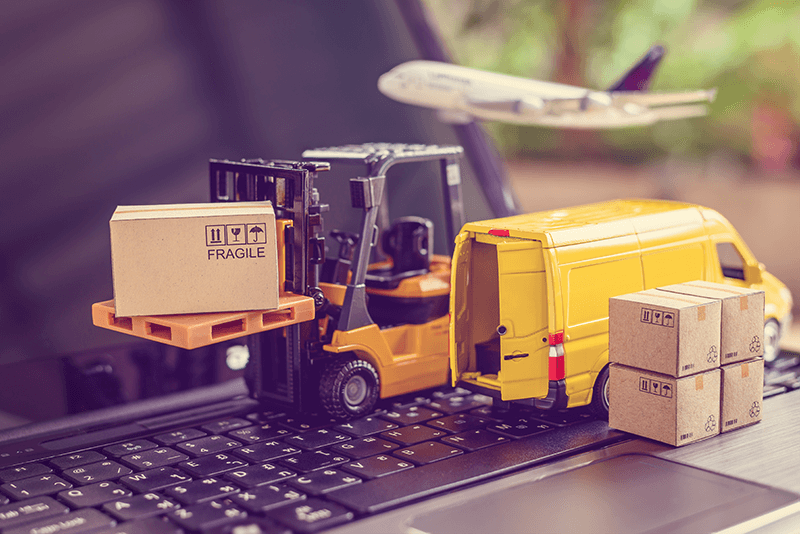
More than 80% of corrugated paperboard can be recycled through recycling. Corrugated paper can be used as packaging for food or digital products, which is relatively environmentally friendly and more widely used.
The corrugated paper has high mechanical strength and can withstand collisions and drops during handling.
Types of corrugated cardboard by number of layers
Corrugated cardboard can be classified into triple wall corrugated cardboard, five-layer corrugated cardboard, seven-layer corrugated cardboard, eleven-layer corrugated cardboard, and so on.
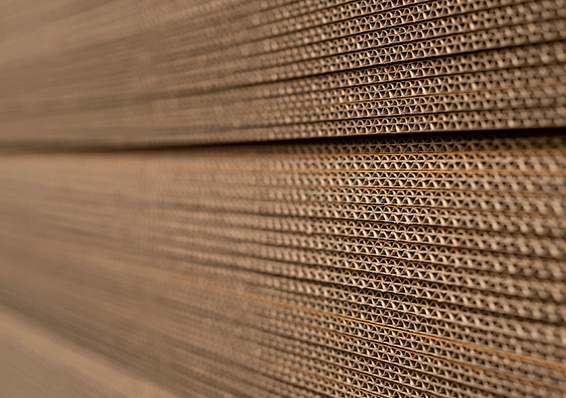
Single wall corrugated cardboard is generally used as a protective layer for packaging, or to make lightweight cardboard or padding for protecting goods from shocks during storage or transportation.
Many products are and beautifully packaged with three-layer or five-layer corrugated cardboard. Beautiful and colorful graphics and images are printed on the surface of corrugated boxes or cartons, which can protect the inner product, promote and beautify it as well.
Seven-layer or eleven-layer corrugated cardboard is mainly used to make packaging boxes for furniture, motorcycles, large home appliances, and so forth.
Corrugated cardboard types by thickness
There are five cardboard flute types types: A flute, B flute, C flute, E flute, and F flute. A flute has the highest compressive strength, B flute has a lower strength, and C flute has a strength between A flute and B flute.
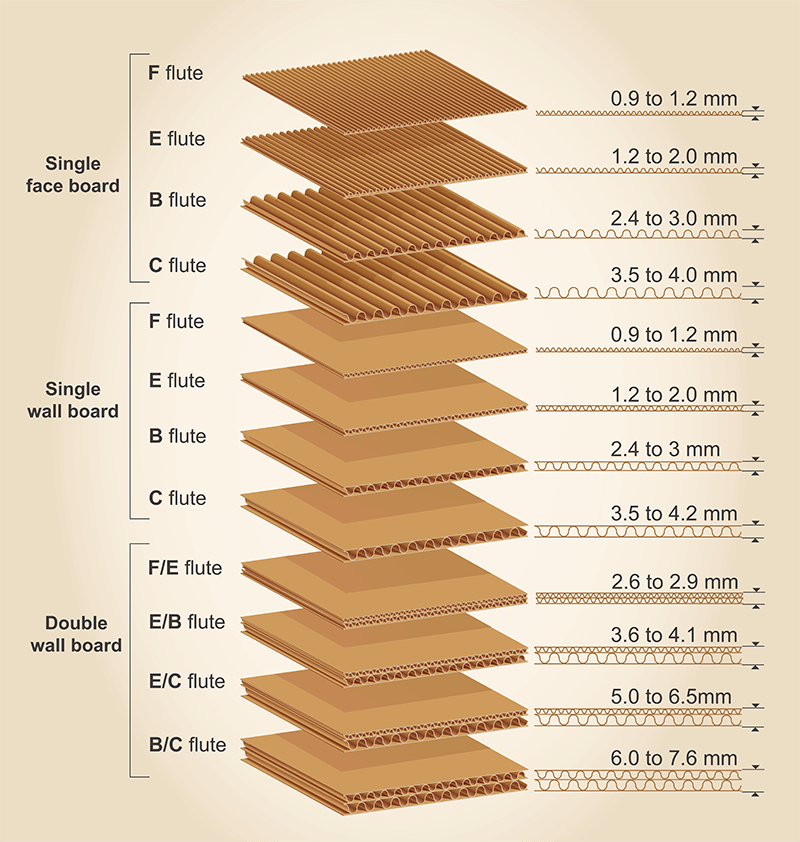
A and B flutes are generally used for transport boxes, and beer boxes are usually B flute.
E flute is mainly used as a single-piece box with specific aesthetic requirements. F flute and G flute, collectively micro-corrugated, are extremely thin corrugations used as disposable packaging containers for food products.
The actual strength performance of corrugated boxes depends on three factors: the characteristics of fluting medium, the two flat liners and the box structure.
When selecting corrugated cardboard materials, to choose a suitable corrugated material, it is essential to take complete consideration of the product weight, the box structure, and the printing needs.
Corrugated packaging printing method
There are commonly two methods of Corrugated packaging printing: flexographic printing and offset printing.
Corrugated cardboard boxes are mostly done with flexographic printing. Directly print water-based inks on the top of corrugated boards through a rubber or a resin board. It is then glued together with a corrugated core and another liner paper to become corrugated packaging material.
It is common to have single-color, two-color printing, and if three to four colors are needed, two printing sets of up to five colors are required.
This type of printing is inexpensive, with low color reproduction, and is suitable for ordinary transport packaging boxes that do not require high printing accuracy. Commonly courier boxes and electrical packaging boxes are printed with flexographic printing.
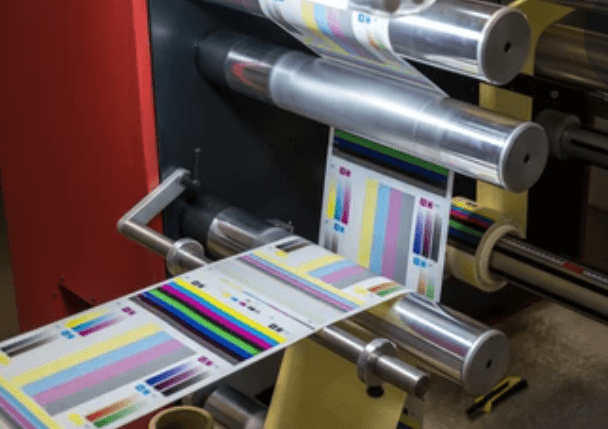
The offset printing process of corrugated cardboard is generally firstly offset printing image on the liner, and then laminated to a single face board.
Because of the widespread use of G flute cardboard, fragile G flute cardboard can be printed directly by the offset printing machine.
How is packaging printed?
The printing process is a entire process of visual, tactile information, printing, and reproduction, which include pre-printing, printing, post-printing process.
It is a collection of photography, art, technology, chemistry, electronics, computer software, hardware technology, and environmental factors of technology.
The packaging printing process is updated more quickly, and we have to keep accumulating and learning new knowledge. The packaging printing methods are as below.
Laminating film
Laminating film includes glossy lamination film and matte lamination film.
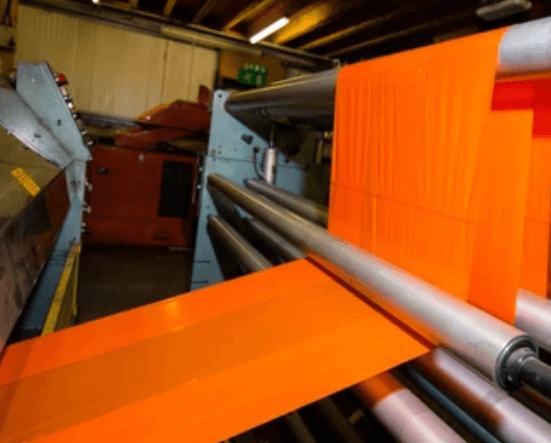
Glossy lamination film needs the laminating machine to laminate the surface of printed materials. It strengthens the toughness of the package and also has the function of waterproof and anti-dirty.
The matte lamination film needs a laminating machine to cover the surface of the printed material with matte lamination film, showing a matte effect. Strengthen the toughness of the package, but also waterproof and anti-dirty function.
Spot color
Gold spot color is the ink with added copper, zinc, and other gold powder. The silver spot color includes aluminum powder in the silver ink.
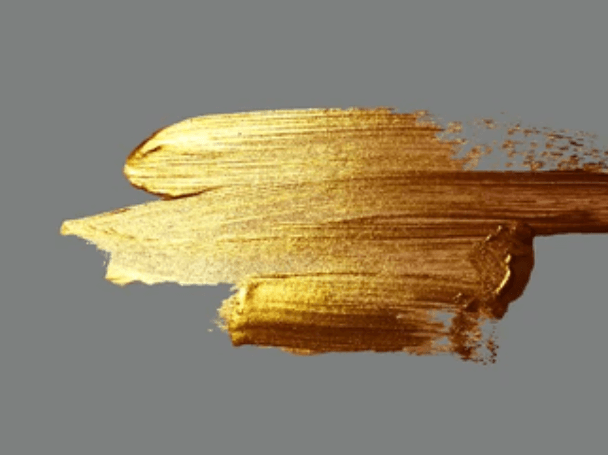
The Four-color printing design adds a spot color will also increase cost, for it needs to choose five-color or six-color printing presses.
Printing spot color is brighter than a four-color. It would be best to mark the spot color PANTONE color value so as not to produce color differences.
Embossing
The embossing process uses a concave and convex mold, and the paper will be sandwiched in the middle under a certain pressure to distort the printed material.
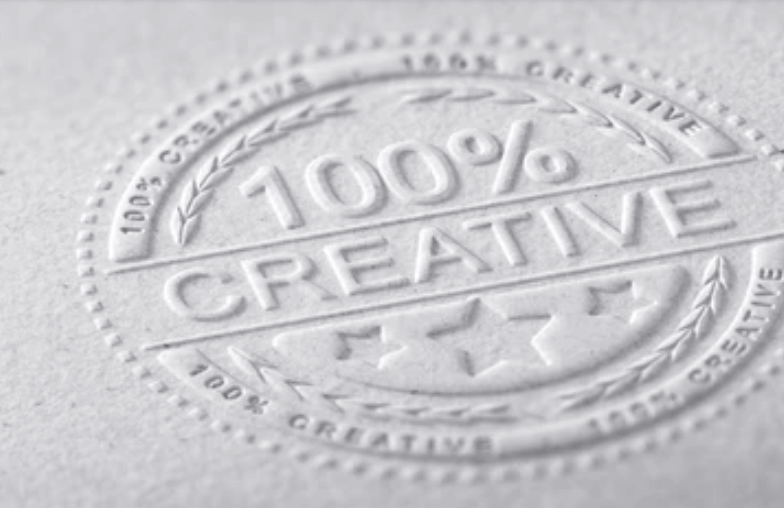
Full bleed embossing, commonly used in high-end gift boxes and other product packaging. And after full bleed embossing, the paper texture sense will become very evident.
UV ink printing
UV ink printing, often used in high-end cosmetic packaging.
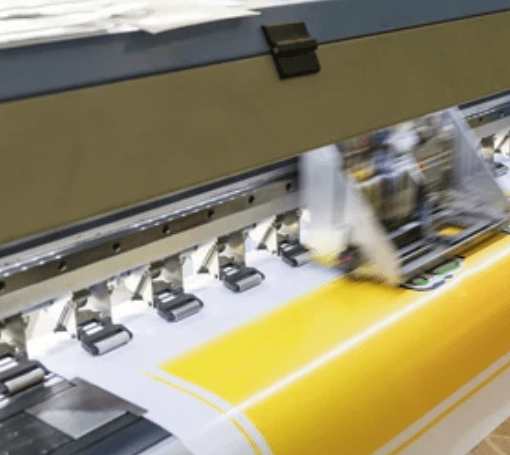
Partial UV varnish screen printing, usually is used in full bleed UV packaging of cosmetics products, showing the contrast between bright and matte texture.
Reverse UV, usually full-page UV, showing the contrast between bright and matte texture, mostly used for cosmetics.
Frosted ink, also known as metal etching ink, the substrate is mostly gold and silver card, with a strong mirror effect of the material. The drying method for UV is by UV curing.
Laser engraving
The diameter of laser beam and spot used in laser engraving are very small, about equal to 0.05mm.
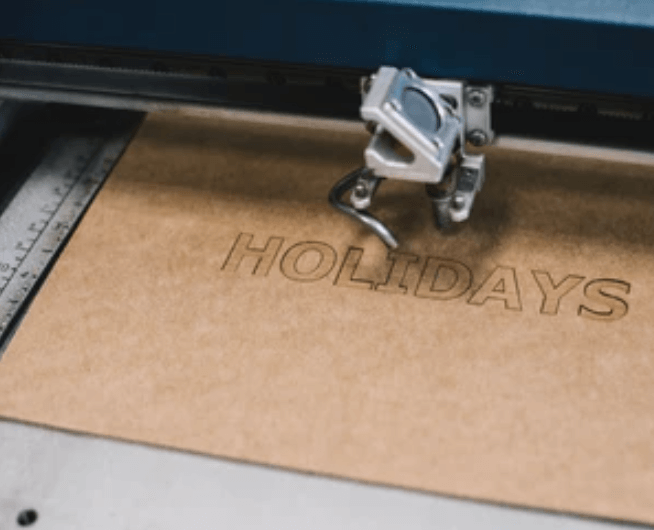
Laser engraving can engrave a wonderful pattern. In the engraving, the paper will be directly vaporized. It will give the pattern a firmer three-dimensional appearance.
Glitter printing
Glitter printing is the printing process by putting 1 layer of glue on the paper first, and then putting sprinkle gold powder or other colored powder on the glue.
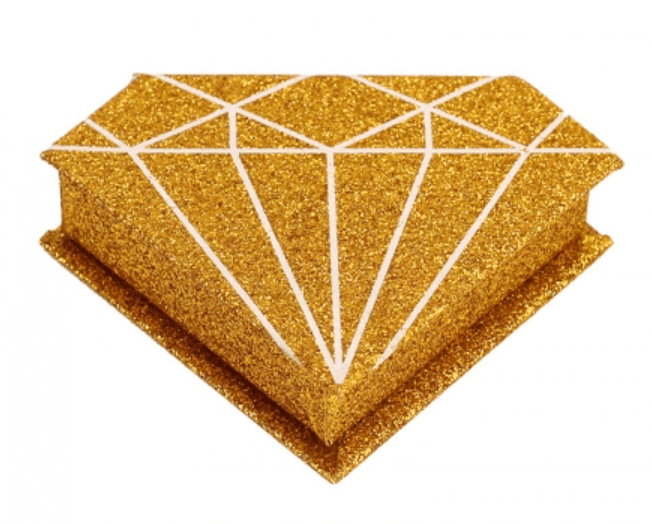
Flocking
Flock printing or flocking is the printing process by putting a layer of glue on the surface of the print, and then pasting the flock. Various color of the flock can be selected.
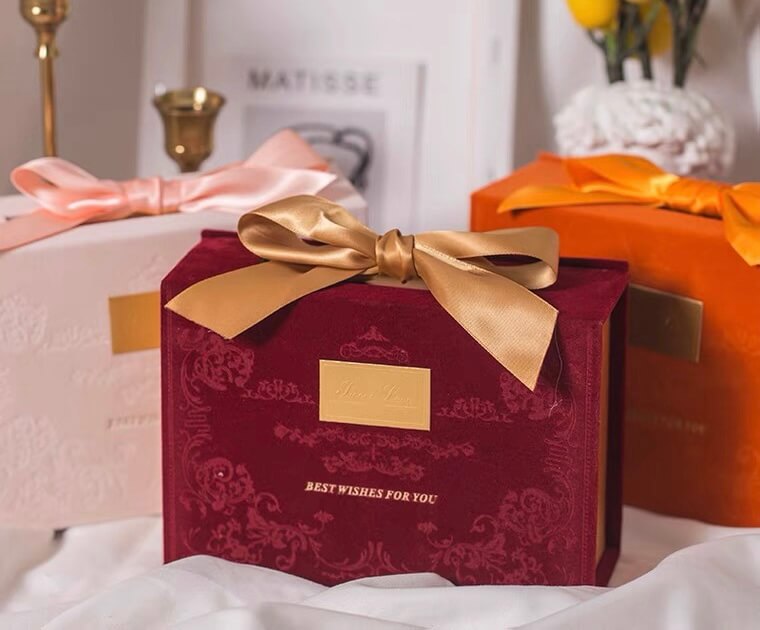
Edge painting
Edge painting is commonly used in high-end business cards and books on the side.
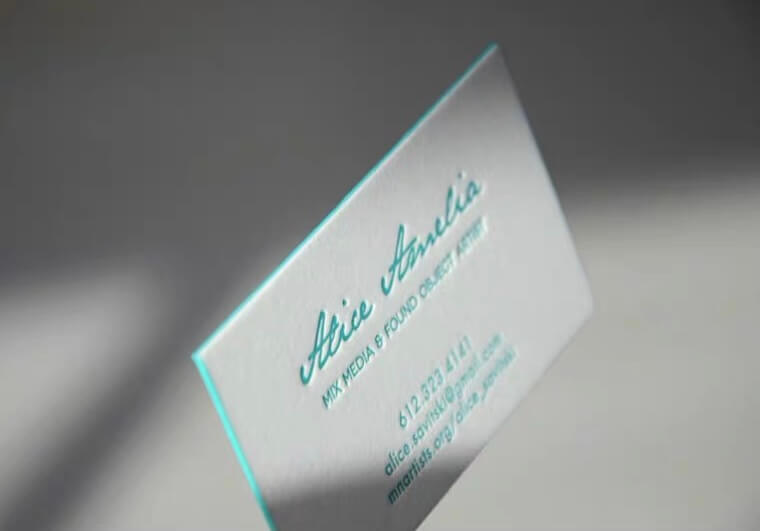
Scratch-off ink
Scratch-off ink is usually used for anti-counterfeiting layer.
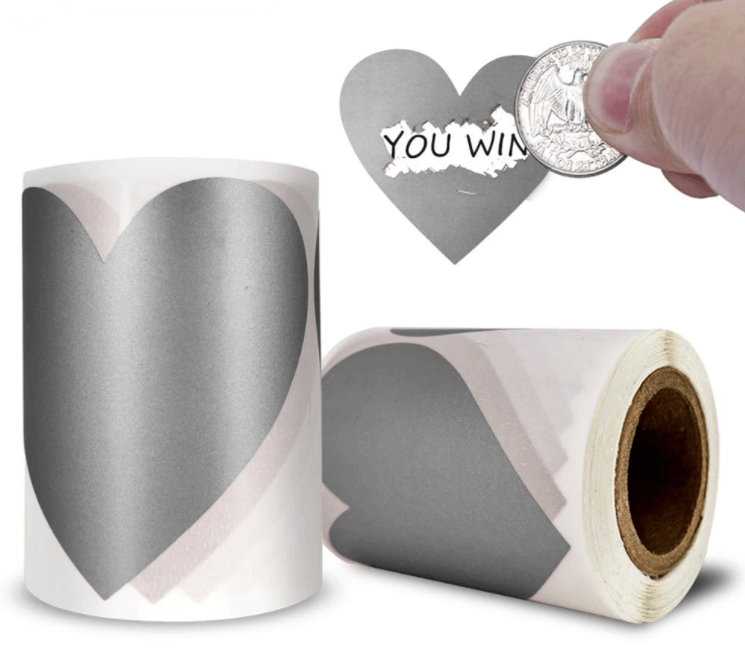